World Class Textile Producer with Impeccable Quality
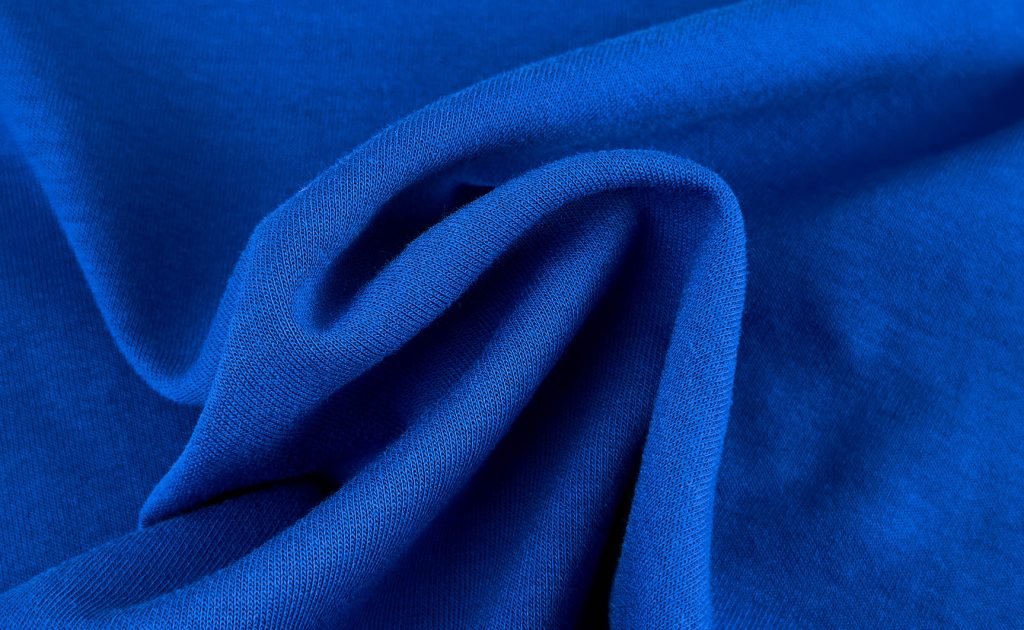
World Class Textile Producer with Impeccable Quality
Double-knit fabrics stand out in the textile industry due to their unique construction. These fabrics have loops on both sides, created using two needles. The interweaving of these loops ensures that the layers are intertwined, preventing separation. The result is double the thickness of standard knit fabrics, boasting a density and stability comparable to woven materials.
Unlike single-knit fabrics, double knits are crafted using a distinctive method. They are produced on a circular knitting machine, where two sets of needles are arranged in a dial above the cylinder. This setup facilitates knitting cycles of knit, tuck, and float, identical to the dial and cylinder. Using two-needle sets eliminates the need for sinkers, a notable deviation from traditional knitting techniques.
The manufacturing process of double-knit fabrics is a sophisticated and detailed operation that combines traditional knitting techniques with modern technology. This process is intricate and crucial to achieving the unique properties that make double-knit fabrics so versatile and durable. Here's an in-depth look at how these fabrics are manufactured:
The journey of double-knit fabric creation begins with the setup of a specialized circular knitting machine. This machine is distinctively equipped with two needles strategically arranged in a dial above the cylinder. This dual-needle system is the cornerstone of double-knit fabric production, allowing for the simultaneous creation of two layers of fabric.
In double-knit fabric production, the configuration of the needles is crucial. The needles in both the dial and the cylinder possess butts and are activated by cams. This setup ensures precise movement and control, allowing for the accurate creation of loops on both sides of the fabric.
Knitting involves three primary cycles: knit, tuck, and float. These cycles are consistently applied to both sets of needles in the dial and the cylinder. The knitting cycle creates the basic stitch, the tuck cycle adds texture and thickness, and the float cycle allows for the creation of intricate patterns and designs. The synchronization of these cycles across both needle sets is essential for the uniformity and integrity of the double-knit fabric.
As the machine operates, loops are formed on the fabric's front and back sides. These loops are expertly interwoven, ensuring that the two layers become intertwined. This interweaving gives double-knit fabrics characteristic density and prevents the layers from separating.
A notable aspect of double-knit fabric manufacturing is the absence of sinkers, typically used in single-knit fabric production. The dual-needle system of the circular knitting machine makes sinkers redundant, as the two sets of needles effectively handle the fabric tension and loop formation.
Ensuring the quality and performance of double-knit fabrics is a critical aspect of the manufacturing process. Textile testing equipment suppliers play a vital role in this phase, providing specialized machinery and expertise for comprehensive quality control assessments.
The finished double-knit fabric is a robust material, ideal for various applications. Its stability and thickness make it suitable for high-quality garments such as pants, jackets, and skirts. Furthermore, the fabric's resistance to unraveling allows for diverse design possibilities, including cutting and sewing into various shapes and forms.
In the realm of weft knitting machines, versatility is vital. Machines capable of producing both single and double-knit fabrics are often utilized. Flatbed machines, which may align two needle beds in a V configuration (V bed machines), are popular choices. These machines excel in producing tubular fabrics or flat panels, which are then assembled into garments. This method minimizes waste and sewing, and advanced technology now allows for the creating of entire garments on these machines.
Double-knit fabrics are not only robust but also versatile in their application. They can be shaped through cutting and sewing without the risk of unraveling, a common issue with woven fabrics. Additionally, steam pressing offers a method to reshape garment parts, such as collars and cuffs, enhancing the fabric's utility in fashion design.
Single-knit fabrics, often used for lightweight clothing like underwear and sleepwear, stretch side-to-side but are prone to edge curling. This characteristic can limit their lifespan but may be seen as a stylistic feature by some. In contrast, double knits have two fabric layers, making them heavier and more suitable for high-quality garments like pants, jackets, and skirts. The double-layer construction adds durability and prevents the edges from curling, extending the fabric's lifespan.
Choosing between single and double-knit fabrics depends on the desired characteristics and applications. Single-knit fabrics are ideal for lighter, less bulky garments, while double knits cater to those seeking thicker, more durable materials for high-quality apparel. Understanding the differences between these fabrics and their manufacturing processes can help designers and consumers make informed choices in selecting fabrics.